Research
Turbulent Atomization
In the context of rising environmental concerns and record-high oil prices, the need for cleaner and more efficient combustion devices becomes pressing. Thanks to the steady progress in computer power and computational fluid dynamics (CFD) methods, computational modeling of combustion systems emerges as a promising tool that can drive the design of future devices. In these systems, fuel is usually injected in liquid form. Atomization of the liquid fuel, or the process by which a coherent liquid flow disintegrates into droplets, represents one of the key challenges that remain to be tackled to make predictive simulations possible. Because atomization governs the size of the fuel droplets, and therefore their subsequent evaporation rate, it will have far-reaching repercussions on many aspects of the combustion process, for example pollutant formation. However, the inherent multi-physics and multi-scale nature of this process limits both experimental and numerical investigations.
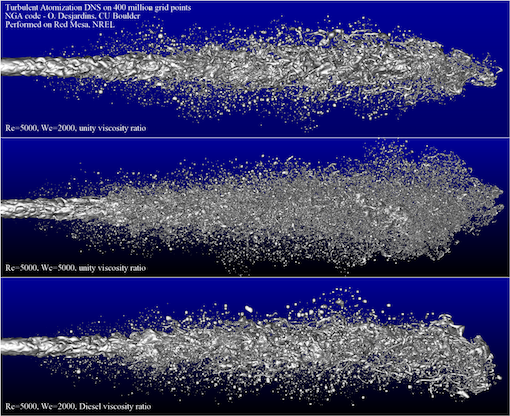
Turbulent liquid jet atomization under Diesel-like conditions, simulated on 400 million cells using NGA.
CTFLab focuses on the development of novel numerical algorithms that enable first-principles simulations of turbulent atomization. Such simulations provide a wealth of data that can be interrogated for the purpose of developing reduced-order models appropriate for use in the industry. The image above illustrates the complexity of the processes we are attempting to capture.
Electrohydrodynamics
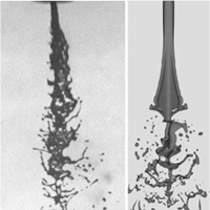
EHD atomization of a kerosene jet, with the experiment on the left and the simulation on the right.
When dealing with small engines, implementing high-performance fuel injection technologies is often too expensive. One approach to small-scale fuel injection is to capitalize upon the benefits of electrohydrodynamics (EHD) and enhance fuel atomization. There are many possible benefits to EHD aided atomization for combustion, such as smaller droplets, wider spray cone, and the ability to control or "tune" the spray for improved performance. Electrohydrodynamic flows and sprays have drawn increasing interest in recent years, yet key questions regarding the complex interactions among electrostatic charge, electric fields, and the dynamics of atomizing liquids remain unanswered. Direct numerical simulations (DNS) of realistic liquid break-up are challenging due to the computational expense involved. High-fidelity numerical simulations should be able to provide assistance in answering questions about the fundamentals and dynamics of EHD atomization.
Additional applications of EHD in our lab include ionic liquids and their use for space propulsion.
Combustion
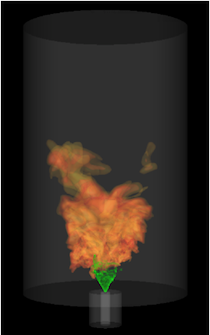
Simulation of turbulent spray combustion in a model combustion chamber.
In gas turbine engines, the liquid fuel must first evaporate before it can combust. Hence, the interplay of liquid atomization and spray vaporization is of paramount importance, for it governs how fuel is supplied to the flame. Similarly, the combustion process is intricately linked to spray evaporation, since the energy required by the phase change is provided by the heat of combustion, and the fuel consumed by the flame comes from liquid vaporization.
A complex flame structure including premixed and diffusion combustion regions has been observed in numerical simulations, which calls for an adequate partially premixed combustion model. Results of preliminary studies have shown that typical gaseous combustion models may not be able to adequately describe multiphase reacting flows. The scalar dissipation rate appears to be significantly modified by the presence of the spray, and this should be reflected in the combustion model.
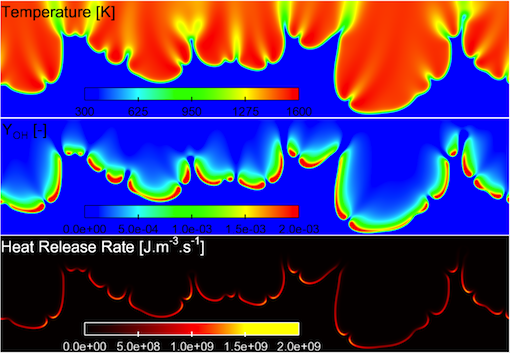
Direct numerical simulation of a thermodiffusively unstable hydrogen premixed flame.
Particle-Laden Flows
Sprays and other dispersed-phase systems can be described by a kinetic equation containing terms for spatial transport, acceleration, and particle processes (such as evaporation or collisions). In principle, the kinetic description is valid from the dilute (non-collisional) to the dense limit. However, its numerical solution in multi-dimensional systems is intractable due to the large number of independent variables. As an alternative, Lagrangian methods "discretize" the density function into "parcels" that are simulated in a Monte-Carlo framework.
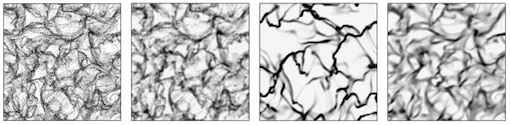
Simulation of particle-laden homogeneous isotropic turbulence. From left to right, Lagrangian particle positions are shown, followed by the corresponding number density field, followed by a corresponding Euler-Euler simulation, and by a quadrature-based moment closure Eulerian-Eulerian formulation.
While quite accurate, as in any statistical approach, Lagrangian methods require a relatively large number of parcels to control statistical noise, and thus are computationally expensive. A less costly alternative is to solve Eulerian transport equations for selected moments of the kinetic equation. However, it is well known that in the dilute limit, Eulerian methods have great difficulty describing correctly the moments as predicted by a Lagrangian method. An alternative approach is to rely on a quadrature-based moment closure in order to formulate the Eulerian equations. Such an approach is capable of handling successfully highly non-equilibrium flows (e.g., impinging particle jets, jet crossing, particle rebound off walls, and homogeneous isotropic turbulence) that cannot be treated with the standard Eulerian approach.
Within CTFLab, several applications that rely on particle-laden flows are investigated. For example, gas-particle flows in vertical risers are used in many industries including gasification/pyrolysis for biofuel conversion, coal combustion, and fluid catalytic cracking. Experimental studies have shown riser flows to be unsteady with large solid-volume fraction fluctuations. Regions of densely-packed particles, referred to as clusters and streamers form, which greatly affect the overall flow behavior and mixing properties. We use a Eulerian-Lagrangian approach to simulate riser flows and better understand cluster formation. The gas phase is solved on an Eulerian grid while each particle is tracked individually.
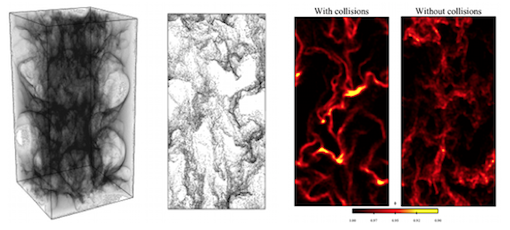
The first image shows a 3D simulation of the flow destabilizing (10.2 million particles, Re=1, Fr=55.5), along with a 2D cross section of the flow at a later time to convey particle clustering. The simulation was conducted on 4 million grid points using 512 processors for approximately one week. The second image shows instantaneous gas volume fraction of the flow with and without collisions.
Verification of Complex Codes
Code verification is strictly a mathematical exercise which demonstrates that the various algorithms have been coded correctly. In order to perform code verification it is necessary to have a benchmark solution for the governing equations so that the error and order of accuracy of the code can be determined under systematic grid convergence studies.
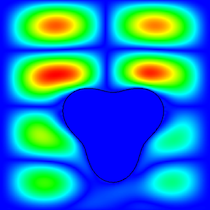
Velocity error for an immersed solid surface calculated using MMS.
Analytic solutions to the governing equations are ideal candidates for benchmark solutions. Unfortunately, sufficiently complex solutions to the Navier-Stokes equations involving non-trivial boundary geometries to test the capabilties of the immersed boundary formulation employed in the code are not available. Thus, the method of manufactured solutions (MMS) is employed to generate arbitrary exact solutions with arbitriary immersed boundary (IB) geometries or multiphase for code verification.
More Information
For more information on joining CTFLab, please see the positions page. For more information on applying to the Sibley School of Mechanical and Aerospace Engineering at Cornell University, please see the MAE homepage.